Selecting the right material for your rubber parts is crucial, especially in industrial manufacturing, where precision and durability are paramount. At RPM, we often get the question: “Which is better for our needs – natural rubber or synthetic rubber?” The answer isn’t straightforward; it depends on various factors, including the specific application and environmental conditions. In this article, we’ll explore the key differences between synthetic and natural rubber, helping you decide on your industrial requirements.
Natural Rubber: The Traditional Choice
Natural rubber, primarily sourced from the rubber tree, has been the backbone of various industries for centuries. It’s produced through rubber tapping, where latex is extracted from the tree and refined into natural rubber. This material is known for its high resiliency, excellent tensile strength, and superior adhesiveness, making it a preferred choice for products that require these properties. However, natural rubber has its limitations. It’s less effective when exposed to light, UV rays, and heat, which can be a significant drawback in specific industrial applications. Moreover, natural rubber production can be more challenging than synthetic alternatives.
Synthetic Rubber: The Modern Solution
On the other hand, synthetic rubber is a product of modern chemical engineering. It’s an elastomer artificially produced in chemical plants, offering a more consistent quality and often a more economical production process. The versatility of synthetic rubber is one of its most significant advantages. It can be engineered and formulated to meet various industrial applications, making it a highly adaptable material. The production of synthetic rubber involves converting monomers into polymers, a process that can be fine-tuned to achieve specific properties. This adaptability makes synthetic rubber an excellent choice for applications where natural rubber might fall short, such as in environments with extensive exposure to oils, chemicals, or extreme temperatures.
Choosing Between Natural and Synthetic Rubber
When deciding between natural and synthetic rubber for your industrial manufacturing needs, consider the specific requirements of your application.
Natural rubber is ideal for products that demand high elasticity and strength.
However, synthetic rubber might be the better choice if your products are exposed to harsh environmental conditions or require more specialized properties.
Both natural and synthetic rubber have their unique advantages and limitations. Understanding these will help you choose the material that best fits your industrial application, ensuring optimal performance and durability.
SYNTHETIC RUBBER TYPE | BENEFITS & DESCRIPTION | APPLICATION |
---|---|---|
Neoprene | Oil & grease resistant; high adhesiveness; high resiliency; high UV-ray & light resistance | Anything with heavy oil or grease exposure; mass transit; door & window seals, HVAC units |
EPDM | UV-ray resistance | Outdoor applications |
SBR (BUNA S) | Most economical synthetic rubber | General-purpose – can be used in many ways |
BUNA Nitrile (BUNA N) | A less expensive, less resistant version of neoprene | Civilian & military vehicles; mobile equipment |
Silicone | High-temperature resistance, food-grade (FDA approved) | Anything that requires high heat or involves exposure to hot temperatures, including cars, cooking, baking & food storage, footwear & electronics |
Viton | High heat; broad chemical resistance | High acid or harsh chemical exposure |
HNBR (Saturated Nitrile) | Physical strength: high retention after long-term exposure to heat, oil & chemicals | Performance-demanding applications in industrial or automotive settings; often used for seals, hoses & belts in cars |
Fluorocarbon | High temperature & excellent chemical resistance | Seals for aircraft & automotive engines; wide chemical exposure situations |
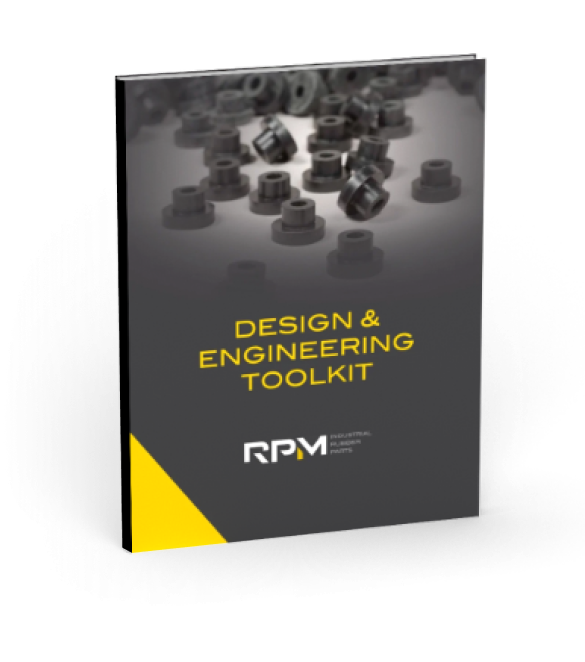
Do you really know everything about designing with rubber parts?
Get a free and valuable resource for finding or custom designing the exact part you need.
Environmental Impact and Sustainability
When choosing between natural and synthetic rubber, it’s essential to consider their environmental impact and sustainability.
Natural rubber is derived from rubber trees, a renewable resource, but its cultivation can be associated with deforestation and biodiversity loss if not managed responsibly.
On the other hand, synthetic rubber, predominantly produced from petroleum byproducts, raises concerns about fossil fuel dependency and greenhouse gas emissions. However, advancements in synthetic rubber production are increasingly focusing on reducing environmental footprints through more efficient processes and using bio-based feedstocks.
For industrial manufacturers committed to environmental stewardship, understanding these sustainability factors is crucial in making an informed decision. By weighing each type’s ecological pros and cons, manufacturers can align their material choices with their sustainability goals, ensuring a balance between industrial needs and environmental responsibility.
Conclusion
The decision between natural and synthetic rubber is not about which is universally better but which is more suitable for your specific industrial needs. By considering the properties and applications of each, you can select the material that will provide the best performance for your products.
If you’re still unsure about the best project choice, our RPM team is here to help. With our natural and synthetic rubber expertise, we can guide you to the right material choice for your unique application.
Related Resource
The Engineer’s 7-minute Guide to Rubber Molded Parts
Our free resource is a quick-reference guide to help you determine if exploring a rubber part is right for your application.