Your Custom Rubber Molding Partner Is RPM Industrial
Rubber is an incredibly versatile and durable material. Consumers can find rubber in almost everything that they use on a daily basis. From car tires to pancake-flipping spatulas, rubber is all around. OEMs and manufacturers leverage the traits of rubber in daily operations. The longevity and durability of machinery and equipment can be enhanced by custom rubber parts.
One of the great qualities of rubber is that it can be crafted to fit specs. Whether special materials are used to support elasticity, control noise, decrease abrasion, or resist heat, there is probably a rubber piece that can fit the bill. Not only can rubber be produced to fit property needs, but it can be easily customized to fit size and shape as well. Rubber is frequently brought to bat to replace discontinued or cost-prohibitive items. Custom rubber molding provides convenient, affordable, and effective solutions.
We are proud to have multiple decades of experience and a universe of satisfied clients that spans the globe.
Rubber Molding
Molded rubber products are useful, time saving and cost effective. There are endless ways to use a compression mold, injection molding or transfer molding to form rubber parts. Silicone rubber has the perfect duality of flexibility and sturdiness. This makes it perfect for vibration control and equipment safety. With quick and easy installation, molded rubber parts and additions last a long time and are resistant to all kinds of challenges.
In South America and Africa, there are trees that contain a latex sap. This sap was discovered by explorers in the early 1700s and sent back to Europe. Natural rubber was used throughout the 1700s and 1800s to make a variety of items such as waterproof coats and erasers. Then in America in 1839, Charles Goodyear dropped a sulfur-treated piece of rubber onto a hot stove. Through this, he accidentally discovered the vulcanization method.
From that moment on, scientists and manufacturers sought reasonable alternatives for natural rubber. The answer arrived in 1930 when a German company created a synthetic rubber that is today known as Styrene-butadiene rubber (SBR). That same year, a U.S. company, headed by Wallace Carothers, produced Neoprene. Even though these synthetic rubbers existed, it wasn’t until the 1940s that they were sold in the United States.
There are two types of rubber: synthetic and natural. Natural rubber has a different chemical composition from synthetic rubber. Because there are many different kinds of synthetic rubber, each with their own chemical composition, let’s start with the chemistry and manufacturing process of natural rubber. This process is complicated and can be difficult to understand. Here is the layman’s version:
- Latex sap-containing isoprene molecules-seeps from a rubber tree.
- As the sap dries, the isoprene molecules attack nearby bonds.
- When these bonds break, the electrons rearrange to form a bond between the isoprene molecules.
- This continues until a long chain of isoprene molecules form, called polyisoprene polymers.
- The sap continues to dry and the polyisoprene chains start to stick together through electrostatic bonds creating rubber.
- When the temperature heats up, the bonds loosen and the rubber becomes sticky and elastic.
- As temperatures cool down, the bonds tighten and the rubber begins to crack.
Once the rubber compound has gotten to this point, it is ready to be vulcanized. Vulcanization takes natural ingredients through another reactionary process, creating a durable and recognizable rubber.
Types of Rubber
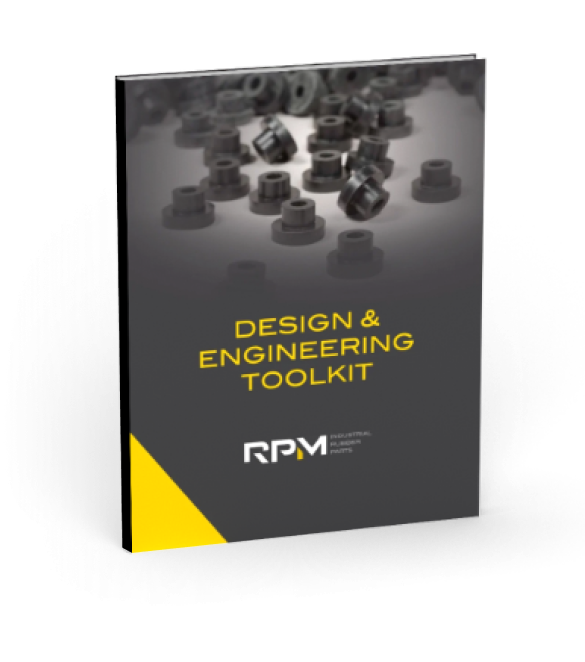
Do you really know everything about designing with rubber parts?
Get a free and valuable resource for finding or custom designing the exact part you need.
Silicone Rubber vs EPDM
Silicone and EPDM are sometimes thought to be interchangeable. This is not true. These rubbers seem similar but have very different properties that change the way they can be used.
Here are the ways in which the two are similar:
- Flame retardant
- Resistant to high temperatures
- Can withstand environmental challenges
- Electricity resistance
- Elasticity maintenance even in harsh temperatures
These qualities mean that both are great materials, but how do they differ? Take a look at this chart to find out more about how they stand up against one another:
Criteria | EPDM | Silicone |
---|---|---|
Production | Synthetic rubber | Inorganic polymer |
Oil and acid resistance | Poor resistance | Moderate resistance |
Common uses | Construction | Automotive | Food & Beverage | Industrial |
Price | Less expensive | More expensive |
Steam and water resistance | Extreme resistance | Poor resistance |
Longevity | Shorter life span | Longer life span |
EPDM and Silicone have many different uses and benefits. There isn’t a categorically superior product. At the end of the day, they have different functional uses that can meet the specs of a given piece of equipment or intended use.
Related Resource
The Engineer’s 7-minute Guide to Rubber Molded Parts
Our free resource is a quick-reference guide to help you determine if exploring a rubber part is right for your application.
Rubber Parts
When consumers choose rubber, they are choosing durability, flexibility, and safety. This is what makes rubber such great material for small parts and additions. There are thousands of rubber parts available to manufacturers and operators.
Rubber is molded through three different methods: injection molding, transfer molding, and rubber compression molding. Rubber parts make equipment safer, more effective, and more controllable.
Molded rubber parts and components can be mass-produced. Most of these products are very generic and adaptable. This way, operators who need specific molded rubber parts can find what they need in a variety of sizes, shapes, and even colors.
Molded Rubber Parts
Molded rubber parts are perfect for quick installation and replacement. They are also cost-effective. Here are some common molded rubber parts and what they do:
- Bumpers: these components help to protect vehicles, equipment, and walls from damage.
- Grommets: these parts are used to cover holes and sharp corners.
- Flanged stem bushings: used to insulate, this molded rubber component protects a variety of equipment and accessories.
- O-Rings: this part is used as a seal.
- Tubing and extruded parts: used in general machinery applications.
- Anti-Vibration pads: reduce noise and friction.
- Suction cups: for a variety of general applications.
- Caps: protect surfaces or components from external damage or impacts.
- Compressor mounts provide isolation to reduce transmission of vibration.
Check out some more molded rubber parts here.
Industries and Use for Rubber Parts
Most industries use rubber in some capacity. Whether it is in manufactured products or production equipment, rubber is an essential material. Some industries use rubber much more than others. Here are examples of those industries and how they use this versatile material:
- Building and Construction: From huge tracks and wheels to tiny tubes and buttons, rubber can be found in virtually every piece of equipment on a construction site.
- Industrial Manufacturing: The machinery that is used for manufacturing contains tons of rubber. Because rubber can withstand a wide range of temperatures and has a long life span, the material is perfect for this work.
- Electrical: Rubber is one of the few materials that does not conduct electricity. This makes it ideal for electrical wiring.
- Food and Beverage: Most food and beverage companies use silicone in their packaging because it can withstand extremely high temperatures. This is why silicone baking utensils are so popular.
Read more on custom rubber molding industries and applications.
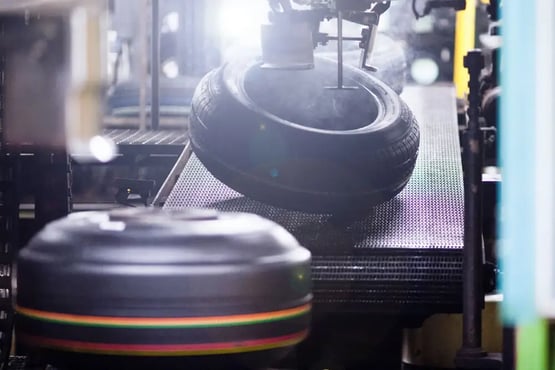
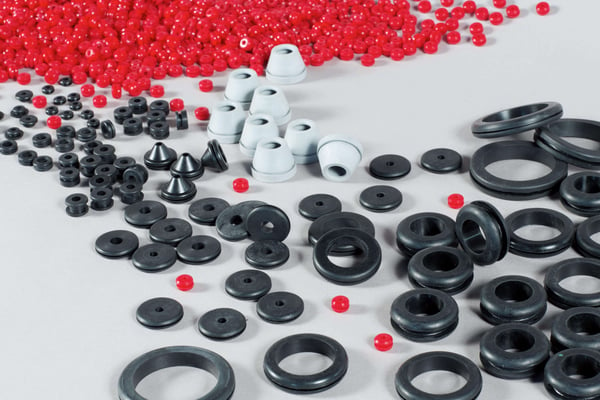
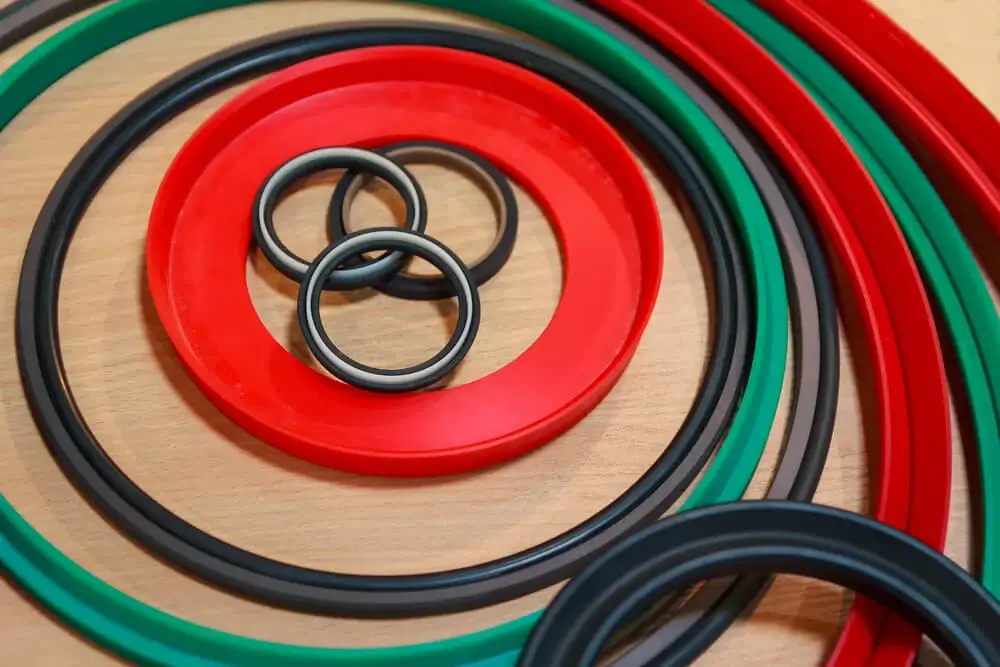
Rubber Products
Using rubber products, instead of plastic, ensures that items last long with minimal wear and tear. Most rubber products are manufactured to be waterproof, heat resistant and flexible. Rubber products range from common household items to complicated mechanical pieces. Rubber is the ideal material for the products that you want to last for a long time under many different conditions.
Rubber Molding Methods
Finished rubber molded products are great for mass quantities. There are numerous ways to mold rubber. One way is through compression molding. Compression molding uses a preform (prepared rubber molding compound) and plates that are sealed tightly. Rubber is added to the mold and then subject to immense pressure to compact and form it. Once cooled, that rubber will hold the shape. This frequently used method works for a number of items.
Go here to learn more about compression molding methods.
Injection Rubber Molding
Another method of molding rubber is injection molding. In some cases, this can be a less expensive way to create molded rubber products. Let’s investigate how injection rubber molding can be achieved and how manufacturers benefit from the efficient, customized options it produces.
Here is how this process works, step-by-step:
- The screw feeder pulls the uncured rubber into the injector.
- The rubber is injected, goes through the runner and gates, into the mold cavity.
- The rubber cures in the mold at high pressure and temperature. This is the vulcanization process.
- The product is removed and the cycle begins again.
Injection rubber molding can be used with uncured natural and synthetic rubber. For silicone products, liquid silicone rubber is injected into the mold instead. This molding method is quick, customizable, and versatile. Injection rubber molding makes few mistakes, saving money on reforms. Molds are also easy to make and adapt which allows companies to offer a wide variety of parts.
History of Injection Rubber Molding
In 1861, Alexander Parkes formulated the first man-made plastic called Parkesine. The plastic had the ability to be molded when heated. While Parkesine did not last long in the industry, it led to other groundbreaking discoveries.
In the 1860s, John Wesley Hyatt produced Celluloid. He discovered that by injecting Celluloid into a mold and curing it, the material would hold its form. Hyatt and his brother Isaiah immediately got to work inventing the injection molding machine. It was finally patented in 1872.
Much later, in 1946, James Watson Hendry built the first screw injection molding machine. This machine dramatically accelerated the process, which meant that manufacturers could make more products in a day than they could before. This machine also allowed manufacturers to prepare the material before it was injected, giving them greater control.
The injection rubber molding machine is constantly being improved to create shorter cycles and superior products.
Chemistry of Rubber Molding
The chemistry of rubber molding actually comes from a process called vulcanization. Depending on the material used, vulcanization can be done in different ways.
Natural rubber and Styrene-butadiene rubber are typically vulcanized using sulfur. Here is how the process works for sulfur vulcanization:
- When Natural rubber or Styrene-butadiene and sulfur are combined, the mixture becomes harder.
- When this mixture is heated, the lead oxide molecules begin to attack and bond with the polyisoprene molecules (chains of Isoprene, the main chemical component of rubber).
- The sulfur bonds with itself and then cross bonds with the polyisoprene and sulfur.
- All of this bonding creates a web of crosslinked molecules, resulting in a tough rubber.
Other rubbers may go through slightly different vulcanization processes. For example, Neoprene is mixed with metal oxides when vulcanized. Silicone can actually be vulcanized at room temperature when mixed with certain solvents.
Technologies for Injection Rubber Molding
Injection rubber molding has remained similar to when it was first invented. While the process has become much more automated, it has not advanced in modern technological ways. The latest improvement has been in control pads. Mostly seen in silicone production, newer injection rubber molding machines allow manufacturers to choose levels of additives on the control pad. This allows operators to have control over the hardness and elasticity properties of the formula.
Tools for Injection Rubber Molding
In order to successfully use injection molding, you will need the right tooling. Here is a list of some rubber tooling that are used for injection molding:
- 3D design software
- Mold developing machine
- Cartridge heaters
- Injection nozzles
- Adhesive
- Cutting machine
- Laser engraving
- Rubber analyzer
- Hardness tester
Top Rubber Manufacturers
Most are familiar with rubber brands such as Goodyear, Michelin, and Firestone. While these may be the most well-known rubber manufacturers, they’re obviously creating products for a specific industry. There is a huge variety of rubber manufacturers outside of the automotive industry who create specialized parts and pieces for global use in all kinds of businesses. Smaller rubber manufacturers have the advantage of offering personalized customer service, custom products, and the best quality.
What Do Rubber Manufacturers Do?
Some rubber manufacturers complete the molding process end-to-end: starting with raw material and ending with finished parts. Others may only process raw material or create molds. The process can be long and complicated.
Here is the full scope of rubber manufacturing (from literal start to finish):
- Collecting: When the rubber is first collected from trees.
- Compounding: Chemicals and other materials are added to the material to give it the proper hardness.
- Shaping: The rubber is shaped through molding and extrusion processes.
- Vulcanization: The rubber is heated and solidifies.
Let’s dive deeper into each step.
Raw Material
The rubber manufacturing process starts with a tree. Raw, natural rubber comes in the form of latex sap from a rubber tree. This elastomer is then coagulated so that it hardens, typically in about 12 hours. Once coagulated, a machine rolls the water out of the rubber. The remaining sheets are dried through smoke or hot air. Once dry, the sheets move on to the next step in the manufacturing process.
Synthetic rubber has an entirely different method of manufacturing. Synthetic rubber is created through polymerization. Essentially, different polymers are combined to create an elastomer. Using different polymers results in different types of synthetic rubbers, which is why so many are used today.
Molds are created through two processes: Computer Numerical Control machines (CNC) and Electric Discharge Machines (EDM).
Read more about elastomers here.
Molds
CNC machines use cutting tools to cut into a piece of material. If a rubber manufacturer wants to use a plastic mold, it could use a CNC machine to create that mold. When dimensions are inputted into the CNC machine, they cut away the piece of material until it fits the dimensions. Some CNC machines are also equipped with laser printing which is another way for rubber manufacturers to create molds.
Electrical Discharge Machines are similar to CNC machines. Instead of cutting, these machines use electric “lasers” to remove parts of the material. When dimensions are entered into the machine, it goes straight to work creating the mold. EDM is typically used for more complicated molds that may require curved edges and specialized shapes.
Prefab vs Custom Rubber
Most rubber manufacturers produce only prefabricated parts. This means that they only sell what they have in their current inventory. One of the defining features of great rubber manufacturers is whether or not they offer custom products. There are many reasons that one may require custom parts. The needed rubber component may be:
- Discontinued
- Not sold internationally
- Too expensive elsewhere
- Not available in the right size or material
Whatever the issue may be, custom rubber components ensure that the safety and usability of the equipment remain intact. Take a look at the custom rubber parts services offered at RPM Industrial Rubber Parts.
Custom Rubber Parts for Automotive
From tires to doors to under the hood, rubber can be found in every aspect of a car. Designers and engineers understand that ingenious ideas require unique pieces. When standard parts don’t fit, custom components could be used for comfortability, safety or general effectiveness. Here is a list of some of the most requested custom rubber products:
- Noise and vibration reduction seals
- Shock absorption
- Electric and wiring
- Protective bumpers
- Window and door seals
- Muffler hanger
- Headlight caps and covers
Custom Rubber Parts for Machines
Heavily used machinery is constantly requiring repairs and part replacements. Even the smallest of components can render the machine useless if not replaced when worn. Some production managers look to add components that reduce noise or to enhance safety. Here are some popular machine rubber parts:
- Edge guards
- Grips
- Mold rubber wheels
- Keyboard and control pad covers
- Mats
- Leg levelers
- Shock absorption
- Gears and joints
- Rubber valves
Custom Rubber Parts for Noise
One of the biggest equipment, vehicle, and machinery complaints is noise. When employees are using these loud tools for hours on end, it can become detrimental to health. OSHA requires compliance with specific decibel levels for workplace safety. Noise reduction custom molded rubber parts are a great way to support employee wellness. Here are some of the most commonly requested parts:
- Conical and center bound mounts
- Mats and pads
- Bushings
- Adhesive rubber foam
- Tubing
Custom Rubber Parts for Vibration
Powerful equipment, machinery, and vehicles often vibrate. This can cause ineffective use and can even imperil operators. Related health issues can include joint pain, bone damage, headaches, and motion sickness. In addition, when components are rattling and making noise it tends to significantly decrease the perception of the build quality of that machine. Take a look at the best custom rubber products for vibration control:
- Anti-vibration pads and mats
- Dampers
- Sandwich, platform, and binocular engine mounts
- Buffers and foots
- Sponge seals
- Couplings
- Sponge cords
Other Uses for Custom Rubber Parts
There are endless uses for custom molded rubber parts. Custom rubber parts play an integral role in the design and experimentation with new tooling, technologies, and machines. Sometimes, custom rubber products contribute to safety or function.
All it takes is an idea. Improvements and modifications to existing equipment, or the inception of novel applications, are both within the scope of customized rubber products from RPM. Even if a person has little to no AutoCAD experience, our engineering team can take the reins and create drawings and designs that will work for each client.
Manufacturing Custom Rubber Parts
Custom rubber manufacturers are problem solvers. If no product on the market perfectly matches equipment or operational needs, companies like RPM can help. All it takes is the part design and dimensions, a custom mold, and expert molding methods.
Custom Rubber Molding Service
There are many custom rubber molding services across the United States. At RPM, we have highly-trained engineers who can find the right solution. Our generations of experience mean that we will quickly understand and execute cost-effective solutions for your business. RPM’s streamlined, efficient process can get you from dream to delivery in no time.
Cost of Custom Rubber Parts
The cost of custom rubber parts varies widely. Factors include size, quantity, complexity, and materials of a project. Parts can range from tens of dollars to hundreds of dollars. Typically, custom rubber parts are cheaper when purchased through rubber manufacturers than through equipment manufacturers. If you are wondering how expensive the custom part that you need will be, ask for an estimate and a price breakdown.
Custom Rubber: Process
Here is how the custom rubber process works:
- First, the client will request a consultation with one of our engineers. During this consultation, the client will explain what they need and detail form and function requirements.
- Next, if the client will submit the design and dimensions. If the client does not have a design, our engineers can create a technical drawing.
- Once we have a design, we can cast a mold. Depending on the requested quantity and size of the part, we will create molds to spec.
- These molds will be filled with rubber and vulcanized. The prototype will be sent to the consumer and once they are satisfied with the part, it can be mass-produced.
- Finally, the finished parts will be shipped straight to the consumer.
Rubber Molding Company
If you are looking for a rubber molding company that provides both standard and custom rubber parts, we can help. RPM Industrial Rubber Parts offers everything that you may need. Here are some of our incredible features:
- Hands-on customer service and engineering team
- High-quality materials
- Thousands of prefabricated parts
- Custom parts in any color, size, function or shape
- Enhanced durability and safety
- National and international shipping
- ISO certified to ensure quality and high standards
We are proud to have decades of experience and a global body of satisfied clients. Our work has helped offset burden, protect workers, extend the life of machines, and enhance productivity. Custom rubber products are an important component of OEM and manufacturing companies.