The process of isolating an object from sources of vibrations is known as vibration isolation. Vibration isolation is used to manage and mitigate unintended vibrations that can waste energy, degraded operation, and significantly limit the operational lifespan of physical components. The basic idea of vibration isolation is to lower the natural frequency of a system than the forced frequency (of the vibration source) and suppress the resonance at the system’s natural frequency. Within the industries and domains that must combat undesirable vibration, several effective methods have been developed for vibration isolation.
The Difference Between Passive and Active Isolation
While both active and passive technology can be used to isolate vibrations from equipment, understanding the difference between the two is vital to effectively resolving vibration issues.
Active Isolation Systems: Active vibration isolation relies on the generation of opposing forces to counteract undesirable vibrations. This is achieved through electronic means, employing sensors and actuators controlled by a sophisticated feedback system. These systems are adept at mitigating low-frequency vibrations by producing disruptive interference to cancel out incoming vibrations effectively. In active isolation setups, a feedback circuit governs the vibration control process, incorporating sensors, controllers, and electromagnetic transducers. Although electromechanical controls might be employed, the fundamental isolation mechanism remains active. The integration of feedback and feed-forward control mechanisms enables active systems to isolate sensitive equipment from extremely low-frequency vibrations that passive systems may exacerbate at resonant frequencies. Active isolation systems are typically intricate and tailored to specific applications.
Passive Isolation Systems: Compared to active vibration isolation systems, passive vibration isolation systems mitigate high-frequency vibration. And due to the simple and affordable nature of materials and components, passive vibration isolation systems are often inexpensive and highly customizable. Passive vibration isolation systems are widespread and span a diverse range of applications. They typically cost less than active vibration isolation systems and their relative simplicity makes them safer and more reliable. Passive vibration isolation uses a passive manner to isolate vibration. These systems utilize materials, like mechanical springs or rubber pads mounted to a vibrating object, and mechanical linkages to absorb and damp mechanical waves. Passive isolation systems can also include elastomers and negative-stiffness components. Passive systems achieve isolation by limiting the ability of vibrations to couple to the item being isolated. A passive vibration isolation system range from simple, like rubber feet on a vibrating object, to as complicated as the shock-absorption mechanisms on an off-highway industrial vehicle.
Bi-directionality: One reason that passive vibration systems are more commonly used than active systems is that they are able to operate in both directions – isolating both the main object from vibrations, but also isolating supporting systems from the vibrations of the main object itself. A passive vibration isolation system can isolate the mass from originating vibrations in the support while isolating the support from originating vibrations in the mass.
Passive Vibration Isolation System Components: A passive vibration isolation system is generally composed of three main elements: an isolated mass (M), a spring (K), and a damper (c). Together, these components work as a harmonic oscillator. The load and spring stiffness define the natural frequency of a passive vibration isolation system. The spring reduces floor vibrations from being transmitted to the isolated payload, while the damper eliminates the oscillation that is amplified within the passive vibration isolation system. Applying this framework for a vibration process to a more complicated vibrating structure is referred to as Vibration Theory. Within this system, the mass and spring determine the natural frequency of the system. Damping causes dissipation and has a secondary effect on the system’s frequency. Maintaining the proper relationship between disturbing frequency and the system’s natural frequency is essential in attaining isolation.
Spring vs. Elastomeric Passive Vibration Isolators: The material used in a passive vibration isolator is often chosen based on the required directionality of its dampening or isolating properties. Often made of steel, springs offer a linear relationship between force and deflection. Meanwhile, elastomers may or may not have a linear relationship between force and deflection, depending on the load. One of the most basic passive isolators is a spring placed between an object transmitting vibration or shock and the item to be isolated from those vibrations or shock. The spring provides energy opposing the impulses against it and absorbs some of this energy as it deforms. For example, how a car’s shock absorber decreases the amount of energy transmitted to the body of the car.
Elastomer Damping Passive Vibration Isolation: Vibration and shock mounts for building foundations, industrial machinery, aircraft components, and automobile engines are all examples of elastomeric isolators. These elastomers are rubber-like materials that deform to absorb mechanical energy. One of the benefits of elastomers over metal springs is that they dissipate (absorb) energy and the spring rate is variable to some degree
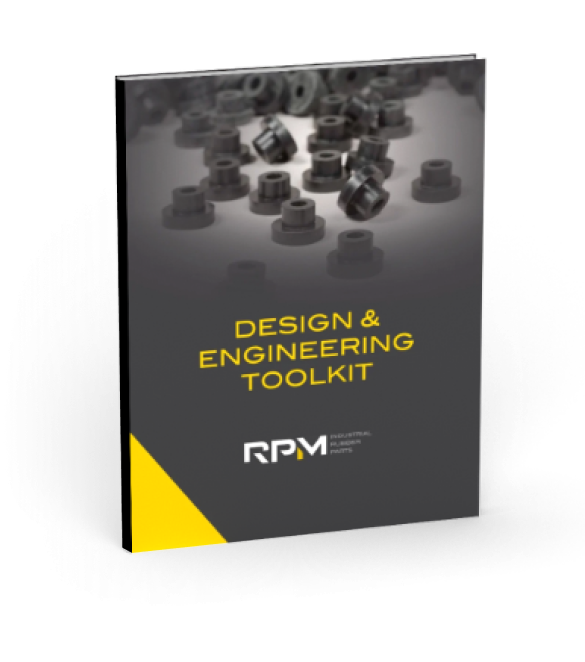
Do you really know everything about designing with rubber parts?
Get a free and valuable resource for finding or custom designing the exact part you need.
How to Select the Optimal Passive Isolation System
Selecting the ideal passive vibration isolation method hinges on an understanding of the specific vibrations requiring mitigation.
There’s no one-size-fits-all passive isolation system; the most suitable solution is the one that effectively addresses your unique requirements. Efficiency can be maximized by considering factors such as application, frequency, direction, and intensity of vibrations. The adaptability and customizability of elastomeric solutions make them particularly versatile.
Obtaining an efficient passive vibration isolation solution can be straightforward and cost-effective when partnering with an experienced provider proficient in passive techniques.
At RPM, our seasoned technicians and engineers boast extensive expertise in developing vibration isolation systems. We ensure that your solution is tailored to effectively tackle your challenges while remaining cost-effective and aligned with your specific needs.
Related Resource
The Engineer’s 7-minute Guide to Rubber Molded Parts
Our free resource is a quick-reference guide to help you determine if exploring a rubber part is right for your application.